Navigating Industry 4.0 Using Legacy Equipment: A Down-to-earth Strategy
Modernizing a factory doesn't always mean scrapping everything and starting from scratch. Even for factories filled with old equipment, digital transformation can be achieved without breaking the bank.
When I paid a visit to an automotive components plant in the Midwest, I found machinery from the 80s right beside systems from the 2010s. The operations manager's sentiment was shared by many: "We can't justify dumping equipment that still performs well just because it ain't got no internet connection." That's smart both for the wallet and the environment.
This mindset aligns with research on sustainable manufacturing practices from Deloitte. The question then, is how to bridge the gap between old-school equipment and the revolutionary promise of Industry 4.0?
Take a look at what's going on in North America—70% of the manufacturing equipment is more than 20 years old, representing billions in capital investment and years of embedded knowledge. Cha-ching!
Giving Old Dogs New Tricks
So, how do you teach an old machine new tricks? Here are some strategies that work:
1. Fitting 'em with IoT Collars (Sensor Retrofitting)
Data's the kingpin in digital transformation. Modern IoT sensors are a great non-invasive way to collect data on equipment conditions without requiring major modifications. Watch a precision metal components manufacturer? They installed wireless vibration sensors on their CNC machines for under $500 per machine. This simple addition helped them detect bearing issues two weeks before failure, turning their reactive maintenance strategy into a predictive one, and reducing unplanned downtime by 37%.
2. Giving Brains to Muscle (Edge Computing)
Small, rugged computers can be installed near equipment to make quick decisions based on collected data without requiring equipment replacement. It's like giving your muscle some smarts. For instance, a paper products manufacturer slapped on compact edge computers to their converting lines to analyze product weight variations in real-time. The system could automatically adjust parameters, reducing waste by 8.2% without coming near their core machinery.
3. Digital Beach Ball (Middleware Solutions)
Modern middleware platforms designed for manufacturing environments can chat with legacy systems, translating old protocols into something your fancy modern systems can understand. It's like a digital translator—a beach ball with brains. A food processing company, for example, connected their 90s-era PLCs with their modern MES system using such middleware. They didn't need to replace the functional equipment. Instead, they invested in software that could bridge the gap between the old and new worlds. The result? A unified digital thread providing real-time visibility across the entire operation for only 15% of the cost of equipment replacement.
Finding the Gold in the Old-timers
Not all old gear is worth pouring resources into. Prioritization requires a clever approach focused on three key dimensions:
1. Production Tightropes (Critical Path Analysis)
Begin by mapping out your production systems to identify the bottlenecks. Invest in digital goodness where it matters most, allocating resources to those elements that dictate your facility's throughput. A comprehensive assessment should include the production impact, quality impact, flexibility limitations, and maintenance history. For a struggling medical device manufacturer, this analysis highlighted that while their molding machines snagged most of the focus, it was actually their assembly systems that were slowing them down. Fix those first, and they achieved a 23% increase in throughput with minimal investment.
2. Valuable Nuggets (Data Value Assessment)
Before investing in digital capabilities, evaluate the potential value of data from each system. Questions to ask: What decisions will this data inform? How quickly will we need it to take action? And what's the financial impact of having it? A chemical processor originally planned a comprehensive sensor deployment across all reactor vessels. After conducting a data value assessment, they determined that monitoring just three parameters on their most variable processes would deliver 80% of the potential improvement. This smart approach saved 65% on their initial digital investment while still enabling critical process improvements.
3. Money Talks (ROI-Driven Implementation)
Gone are the careless days of just throwing money at problems. In brownfield transformations, every initiative must have its ROI justified. Develop clear ROI models for retrofit options that include initial investment, ongoing costs, expected benefits, and implementation risks. One manufacturer established a tiered implementation approach where only retrofits with a projected ROI of less than 12 months were approved in phase one. This disciplined approach created buy-in as initial projects delivered visible results, kickstarting later phases.
Creating a Technology Roadmap for Step-by-Step Transformation
Successful brownfield transformations are about stepping stones, not wholesale revolutions. Here's what a good roadmap looks like:
1. Function over Form (Capability-Based Planning)
Focus more on defining the capabilities the organization needs to develop than on technology implementation. This approach allows you to evolve technologies as time goes on while staying focused on the business benefits. Goals for Phase 1 could be real-time visibility into production status and performance, followed by condition-based maintenance, closed-loop quality control, and dynamic production scheduling in later phases.
2. Layer Cake (Layered Architecture Development)
Build your digital infrastructure in distinct layers that can evolve independently:- Connection layer (sensors and basic connectivity)- Data management layer (storage, normalization, and basic processing)- Application layer (analytics, visualization, and user interfaces)- Integration layer (system connectivity and information flow)
3. Developing the Talents (Skills Development Integration)
Human abilities are often overlooked in brownfield transformations. A good roadmap integrates training, change management, process improvement, and leadership development alongside new technologies.
In the end, those with the wisdom to take old equipment and make it sing in the digital era will reap the benefits of Industry 4.0—improved visibility, enhanced flexibility, optimized maintenance, and data-driven decision making—all while holding on to their existing capital investments.
The path to Industry 4.0 doesn't require throwing everything away. With strategic thinking, smart prioritization, and a focus on the business capabilities that matter, manufacturers can leverage their existing infrastructure to transform their operations one step at a time, as highlighted in the World Economic Forum's white paper on digital transformation in manufacturing[1][2].
Enrichment Data:
- To effectively integrate digital capabilities into legacy manufacturing equipment for a cost-effective Industry 4.0 transformation, consider the following strategies:
- Sensor Retrofitting
- Edge Computing
- Middleware Solutions
- Data Value Assessment
- ROI-Driven Implementation
- Layered Architecture Development
- Critical Path Analysis
- Skills Development Integration
1. The collaboration of old machinery with modern technology can be facilitated through sensor retrofitting, edge computing, middleware solutions, data value assessment, and ROI-driven implementation.
2. Sensor retrofitting, like installing wireless vibration sensors on CNC machines, can provide valuable data without requiring significant modifications.
3. Edge computing equips equipment with small, rugged computers to make quick decisions based on collected data without necessitating equipment replacement.
4. Middleware solutions function as digital translators, bridging the gap between legacy systems and modern ones, allowing machinery to communicate effectively.
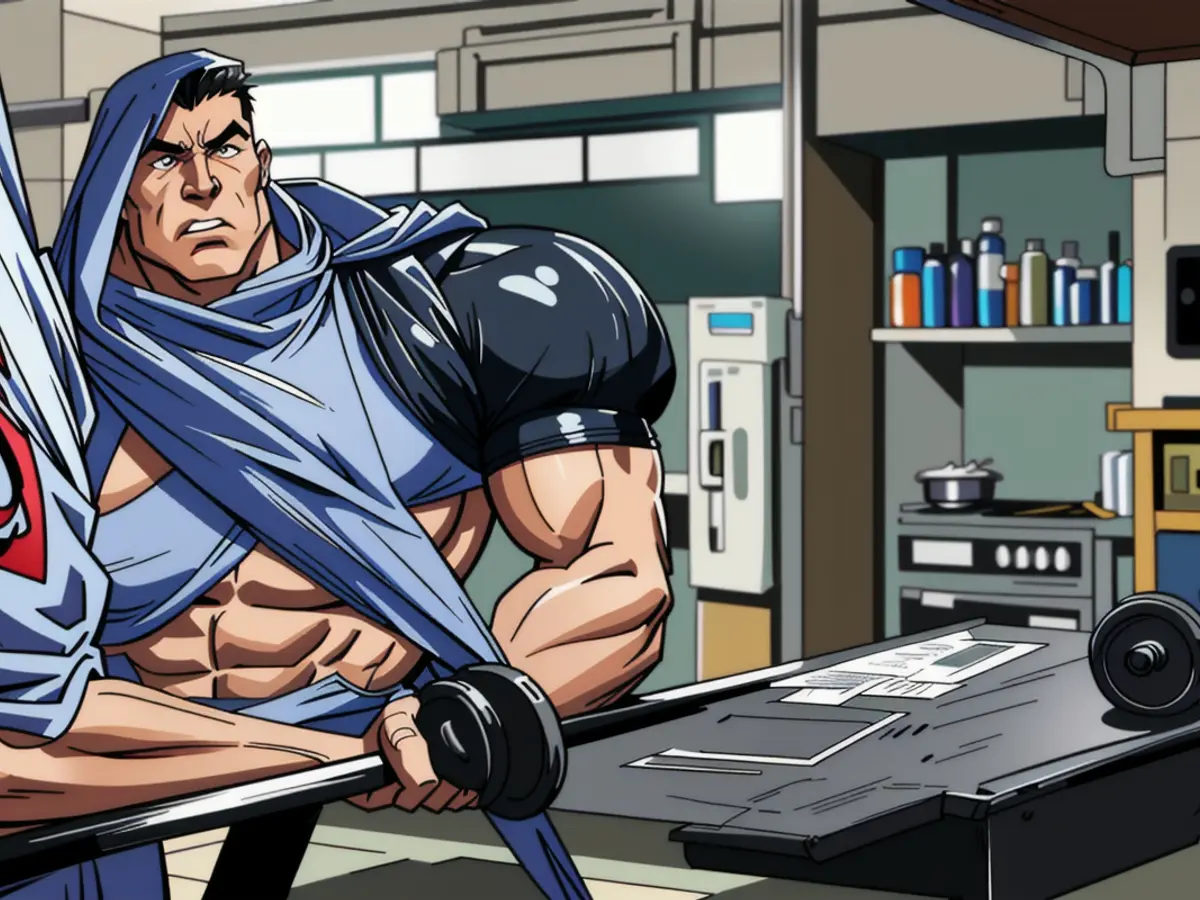
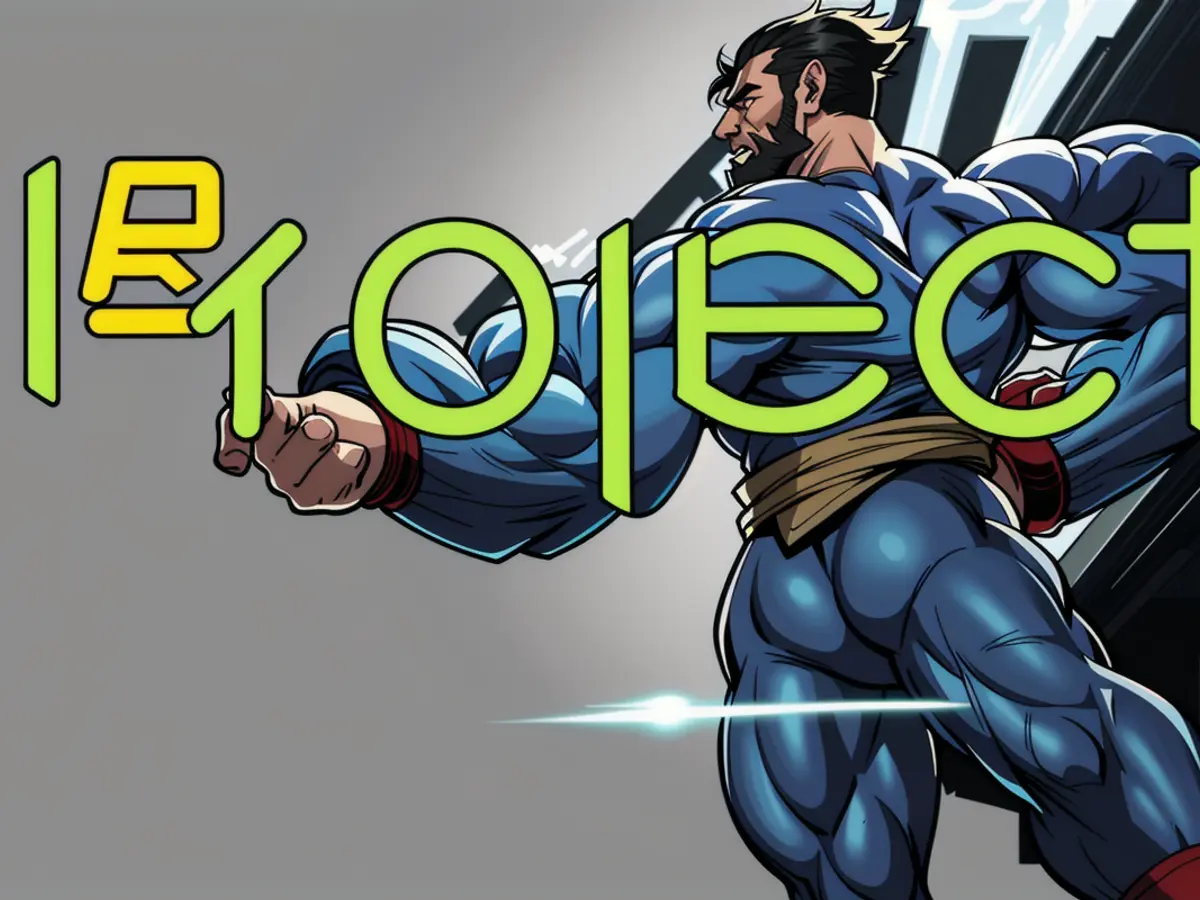
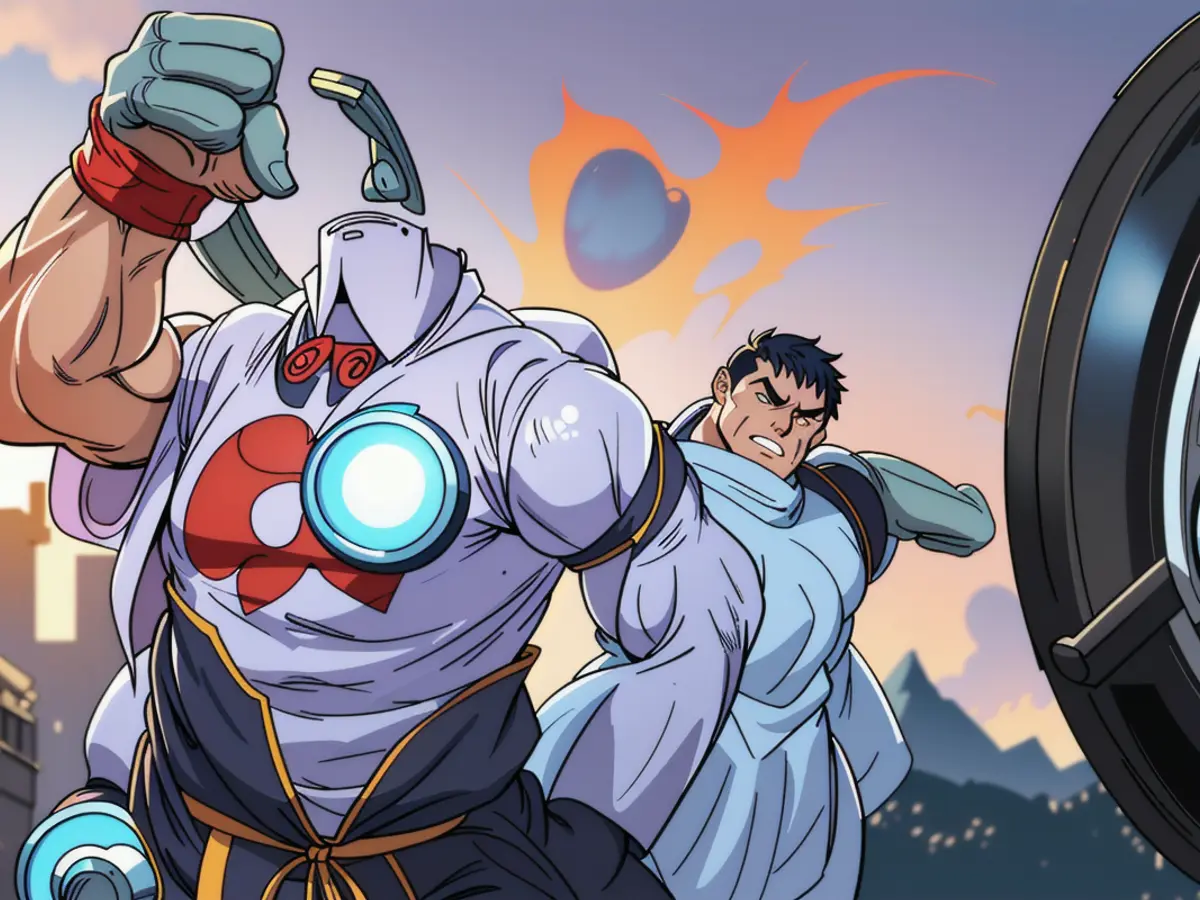