Practical Effects of Producing Artificial Intelligence and Enhanced Reality Systems
June 3, 2025
12:00 PM ET / 11:00 AM CT / 9:00 AM PT / 5:00 PM GMT
Duration: 60 minutes
Sponsor: Dassault Systèmes
Already registered? Click here to log in.
Unveiling the True Impact of AR and AI in Manufacturing: Separating Reality from Hype
It's time to dodge the marketing fluff and delve into the brutal truth about augmented reality (AR) systems and artificial intelligence (AI) systems, their practicality, and their true ability to transform your factory floor. Are they truly resolving the daily hurdles you face? Can your run-of-the-mill company get them to work like a charm? Let's find out!
Join us in this session to shed light on the real-world successes of AR and AI, demonstrating how these technologies can revolutionize manufacturing processes by tackling problems such as efficiency, precision, and adaptability in industrial equipment manufacturing.
During this discussion, you'll:
- Peek under the hood and explore how AR and AI solutions can genuinely impact manufacturing processes
- Learn from compelling customer success stories featuring actual use cases
- Gain practical insights, tangible examples, and a clear understanding of whether investing in AR and AI is the smart play for your business
Speaker
Mike Bradford | Director - DELMIA Strategic Business Development and Marketing | Dassault Systèmes
Mike Bradford boasts a staggering 30-year career in Manufacturing and IT, with experience unparalleled in Management Consulting, Software Consulting, Business Ownership, and part-time college instruction. He currently serves as the Sr. Industry Process Consultant for Transportation & Mobility in the DELMIA Center of Excellence.
An ASCM (formerly APICS) and AIAG member, Mike`s contributions extend beyond the industry, speaking at numerous workshops and conferences and publishing in trade magazines.
Sponsored by:
Proven Successes in Manufacturing
1. Operational Efficiency Gains
- Boeing: Sliced wiring installation time by 25% with AR-guided assembly
- BMW: Slashed inventory errors by 33% and ID time by 22% using AR glasses
- Samsung: Guaranteed 95% equipment uptime with AI-driven predictive maintenance in semiconductor fabs
2. Quality Control Breakthroughs
- Bosch: Inspects nanometer-scale solder points, reducing electronics defects
- Ford: Spots tiny paint defects to ensure perfection in production
- Whirlpool: Cracked down on product inconsistencies with AI-driven RPA bots
3. Workforce Training & Safety
- Volkswagen: Shed light on complex assembly tasks with VR simulations
- Airbus: Illuminated the way with HoloLens 2 AR overlays for technicians
4. Cost Savings
- Porsche: Bagged 30-40% capex savings on custom AR-guided AGV assembly lines
- Bosch (Energy): Turkey-slapped the electric bill with 18% energy savings through AI-optimized processes
Marketing Hype vs. Reality
Common Exaggerations
- "Fully Autonomous Factories": More about task-specific automation (e.g., Whirlpool's RPA bots) than end-to-end autonomy
- "Zero-Defect Guarantee": Physical limitations still exist, no matter the AI solution
- "Instant ROI": Results, yes, but at a high initial cost in hardware/software
Challenges for Average Companies
- Data Infrastructure: AR solutions demand clean data within IoT networks, not always available for smaller manufacturers
- Skill Gaps: Specialized training, such as with HoloLens, required for technicians
- Customization Costs: Off-the-shelf AI and AR tools often fall flat when they don't fit niche processes, necessitating pricey customization
Key Differentiators for Success
| Factor | Top Performers | Average Companies ||--------|----------------|--------------------|| Data Maturity | Real-time IoT sensor networks | Siloed legacy systems || Use Case Focus | Targeted problems such as Porsche's custom AGV lines | Broad, vague goals || Change Management | Workforce upskilling programs | Ad-hoc training |
While AR/AI solutions produce tangible benefits when wielded strategically (e.g., Boeing's assembly lines), smaller companies often struggle with implementation due to resource constraints and overestimation of out-of-the-box solutions. Success is achieved through strategic implementation, partnering with domain-focused vendors, and honing in on high-impact use cases.
- The impact of augmented reality (AR) and artificial intelligence (AI) systems on productivity within the manufacturing industry has become a topic of significant discussion, with many companies aiming to leverage these technologies to enhance their production processes.
- In the real-world manufacturing scenario, AR and AI systems have demonstrated impressive results, such as Boeing slicing wiring installation time by 25% with AR-guided assembly, or BMW slashing inventory errors by 33% with AR glasses.
- However, it's essential to separate marketing hype from reality when it comes to the capabilities of AR and AI in manufacturing. For instance, the idea of fully autonomous factories often refers more to task-specific automation than end-to-end autonomy.
- Implementing AR and AI solutions presents challenges for average companies, including the need for a well-structured data infrastructure, the training of technicians for specialized tasks such as HoloLens utilization, and the high costs associated with customizing off-the-shelf AI and AR tools to fit niche processes.
- Success in integrating AR and AI technologies into manufacturing processes relies on several key factors, such as data maturity (e.g., real-time IoT sensor networks), a focus on specific use-cases (e.g., Porsche's custom AR-guided AGV assembly lines), and effective change management strategies, such as workforce upskilling programs and targeted training programs.
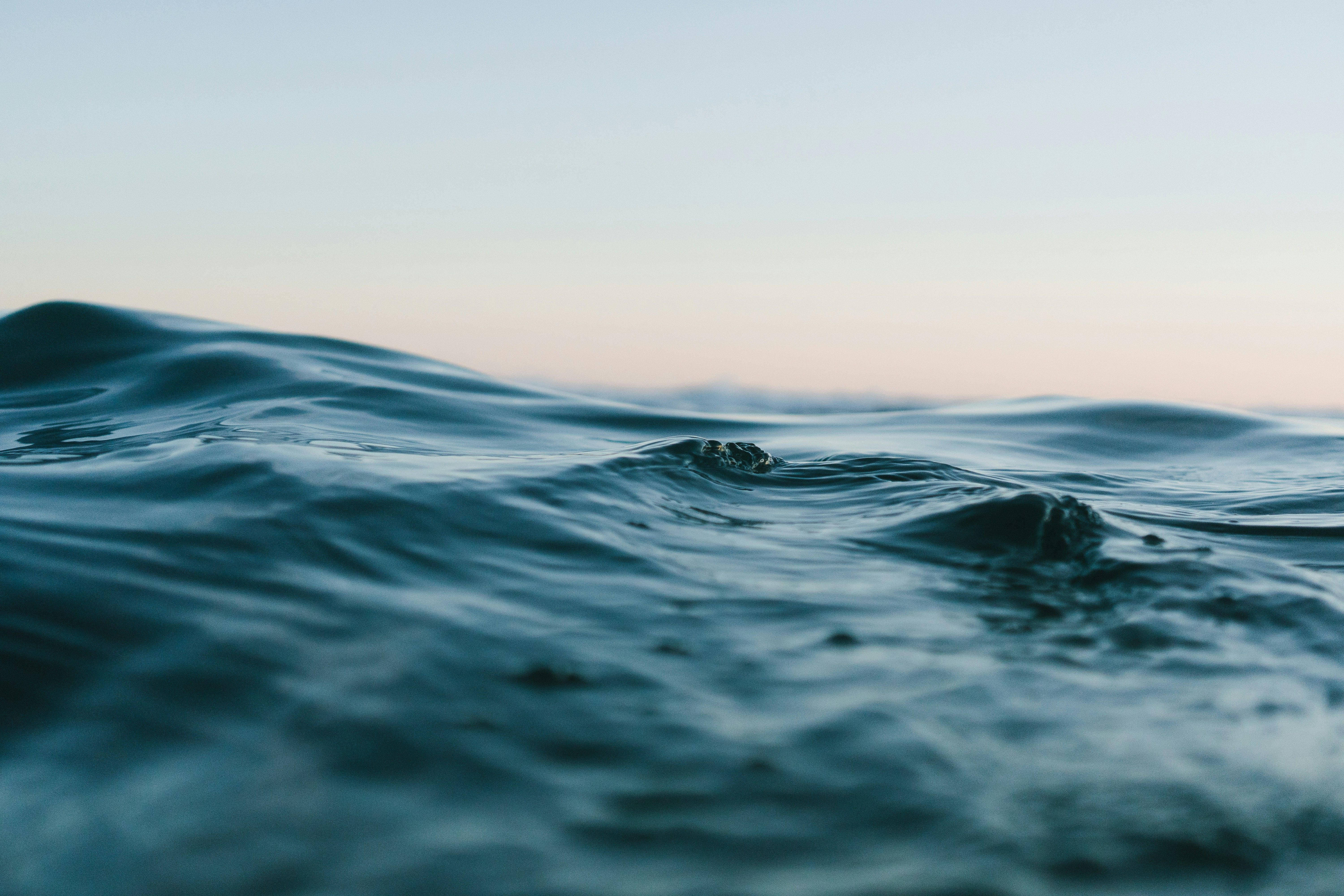
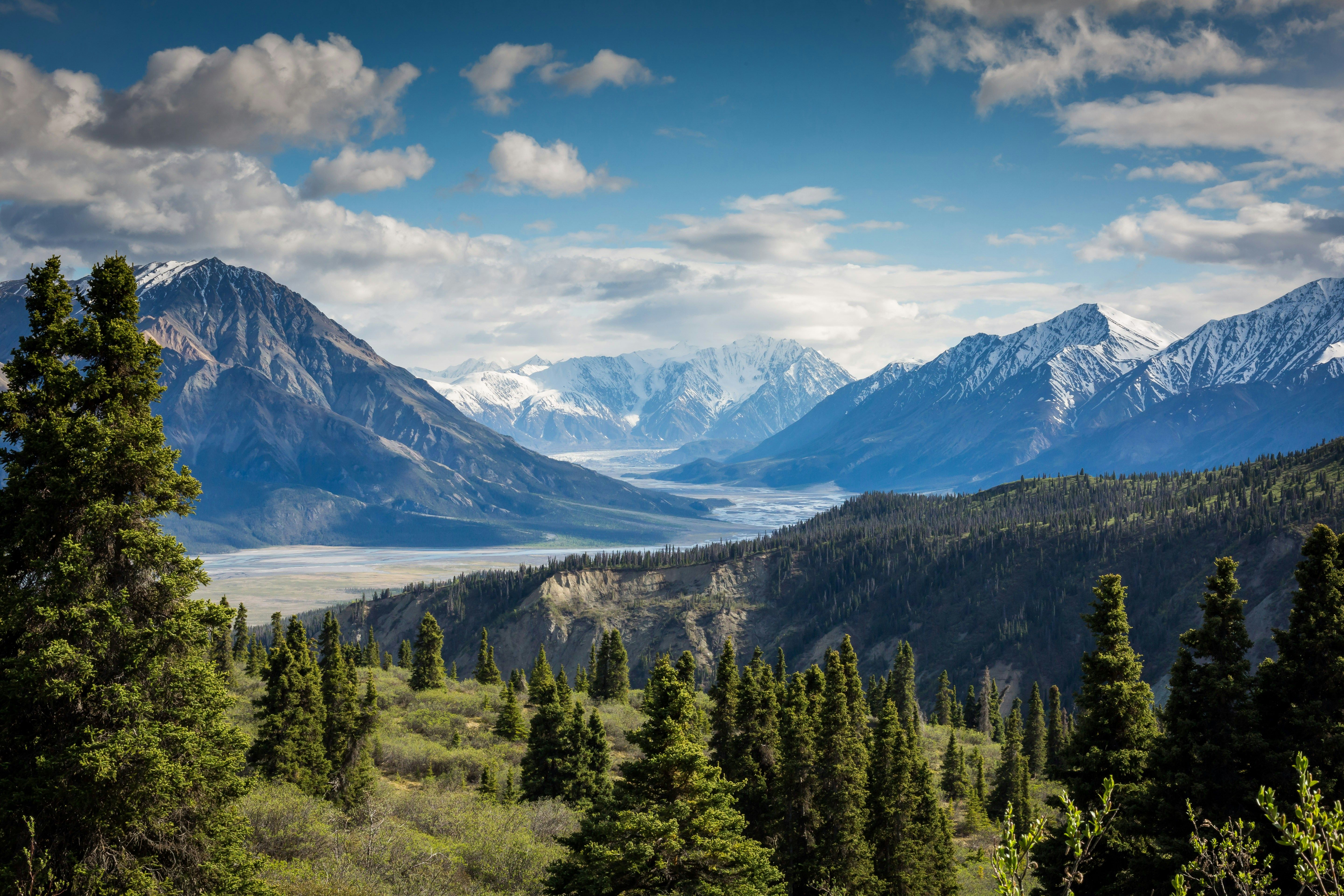
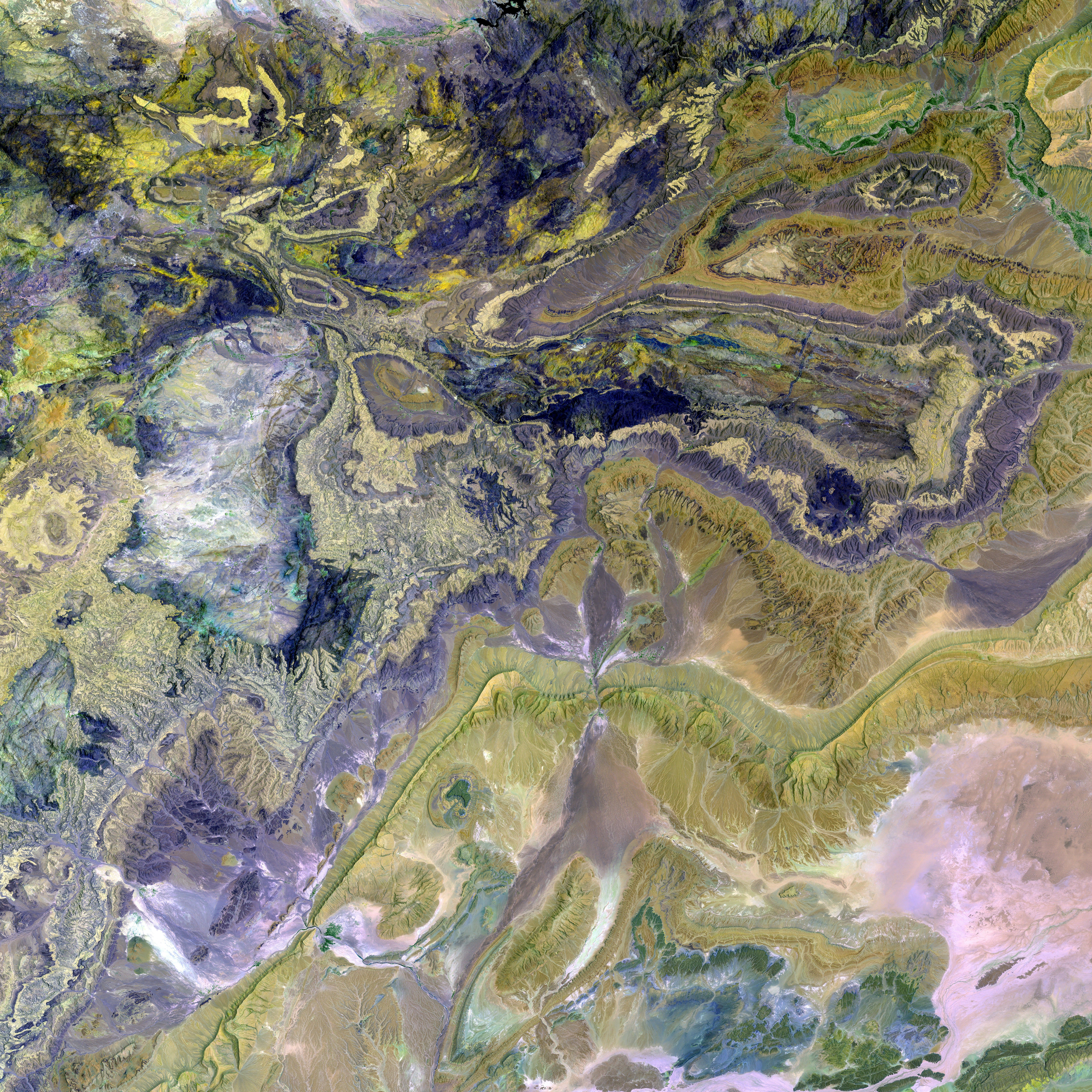